What Is a Hot Pour Skincare Formula?
Waterless, water-free or anhydrous beauty refers to skincare and cosmetic products that are formulated without water. Instead of water, they use various butters, oils or waxes, and oil-soluble actives as ingredients. Hot pour, or hot fill, formulas primarily consist of a wax base in place of a water base and can be called anhydrous, waterless, or water-free.
The wax base is a major differentiator in these formulas. There are many different types of waxes in the market that provide a wide variety of skin benefits from skin better adhesion and moisture. For example, Beeswax is popular because it is a natural honeybee product from beehives and has several skin and lip care benefits, including working as a natural moisturizer for hydrated and soft lips. Carnauba is a popular choice for brands that check the vegan option. It provides a glossy finish while Lanolin and paraffin help soften and moisturize. Waxes like Ozokerite firm up the base of a natural deodorant thickness and texture. New innovations for wax blends are being developed to continue evolving the options available in this space.
Anhydrous wax products have an advantage over water-based products since water-based products can remove the protective natural oils from the skin as the water evaporates. The consumer is left with all the synthetic emulsifiers, chemical colorants, toxic fragrances, and preservatives that are added. Skin becomes sensitive, red, inflamed, flaky, and can even start breaking out.
What are the advantages of the hot pour process?
Hot pour formulations can have a longer shelf life because of the blending process that doesn’t include water and oil phases which can separate over time. They also are less prone to bacteria growth since they typically don’t have water, so there is little for the microorganisms to feed off.
Waxes can help products maintain their function and quality acting as an emulsifier for other ingredients. They prevent oils from separating within the product and keep other ingredient substances together. This makes a more homogenous finished good which translates into customer satisfaction over the active life of the product.
Waxes are essential for holding a stick shape that can be made into a bullet shape for lip balms and lipsticks. This allows the product to include patterns and shapes in the product itself as well.
What special steps are involved in the hot pour and filling process?
Hot pour ingredients are batched together in phases that are set at different temperatures, agitations, and lengths of time. It is typical to have between two to three phases to ensure that the wax bases are fully melted and blended to create a homogeneous emulsion. Phases are grouped together by temperature and optimal agitation type, which is based on the properties of each of the individual raw materials. Each phase typically has an initial set and end target temperature that ensures each phase is ready for the next one, for example, mixing for 30 minutes after ingredients are initially blended together.
What are the benefits of a hot pour product to the brand and consumer?
Typically, hot pour products are more concentrated than their water-based counterparts since they tend to contain higher levels of active ingredients. Since they aren’t diluted and can be more sustainable. Waterless formulas significantly decrease water consumption which builds to preserve this endangered and vital natural resource.
The more water a product contains, the more preservatives it needs to keep bacterial growth at bay. Anhydrous formulas can swap out high amounts of synthetic preservatives with more natural or earth-friendly preservatives. Parabens, often used in water-based products, are preservatives that hinder the growth of microorganisms and give products a longer, more stable shelf life, but they have also been connected to illnesses and health problems.
No water in formulas usually means smaller packaging made of significantly fewer materials which can reduce shipping weight, and space the overall carbon footprint of the product. There is typically less product testing required if no water is present in the formula, tests for micro-organisms are not needed which can make production costs less.
How does a FP Labs hot pour product differ from other contract manufacturers that cold pour?
Waxes have many benefits for the skin but can be tricky to maintain consistency during production. Both hot and cold pour use tanks, agitators (mixers), filling lines, etc., but the cooling stage is one of the big differences between the two. Each wax-based formula needs to be cooled according to the specific properties of that formula. FP Labs has various cooling tunnels that hit products with either one or two cooling stages to ensure the product is at the proper temperature before capping. Issues that can occur during cooling are cracking, bubbling, concave appearance with top fill container, and crusting which makes initial application rough upon application with skin.
Capping a product too quickly or not quickly enough can create issues with opening the product in its final stage as well. The process engineers are experts in this area and ensure that through production we get an even and consistent finished product.
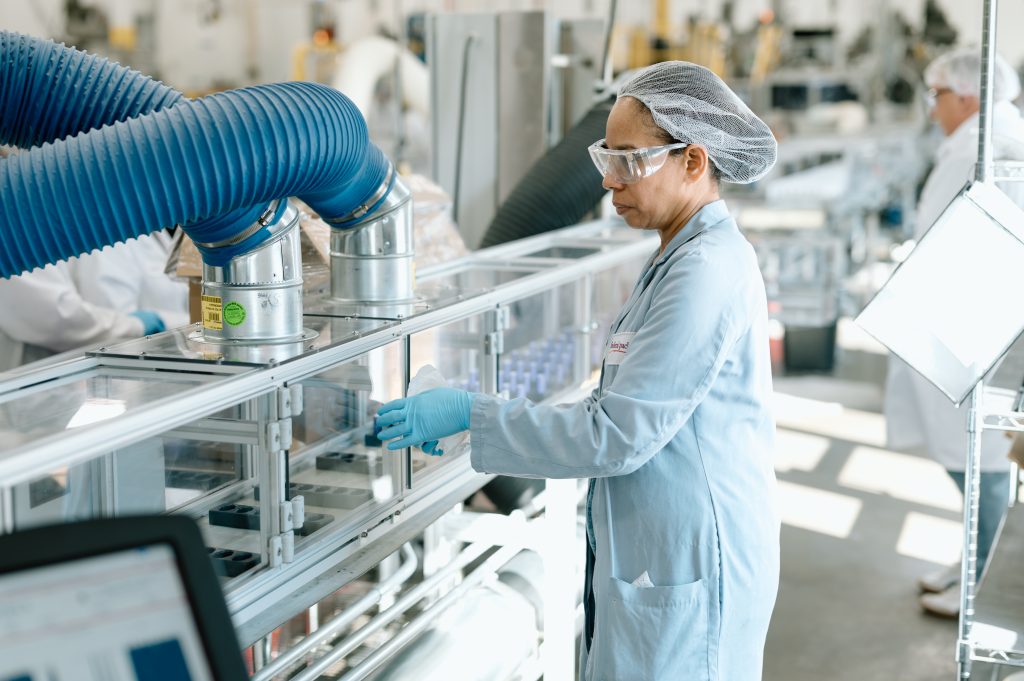
What products are the best for hot pour production?
Products that lend themselves to hot pour are lip balms, lip glosses, deodorants, sunscreen anti-chafe sticks, skin care balms and hand salves, hair pomades, and beard waxes as well as nail and cuticle balms. We’ve also seen many pet products in this space for paw, skin, and snout-soothing wax-based products.
What techniques does FP Labs employ that produce the highest quality hot pour products?
It can be difficult to blend waxes and powders together. FP Labs has the proper equipment to ensure that powders are fully integrated into wax bases and do not create colloids (pockets of powder not properly mixed in).
FP Labs utilizes double-insulated tanks that use circulated water maintained at the completed formula temperature from final blending and compounding through complete line filling. Our filling lines all have heated lines and nozzle heads that also maintain that temperature up until the point it is inserted into the finished container.
Our filling lines also have a glazing option that can be used depending on the formula to help with concave appearances in top fill containers as well as crusting issues to make skin application smoother.
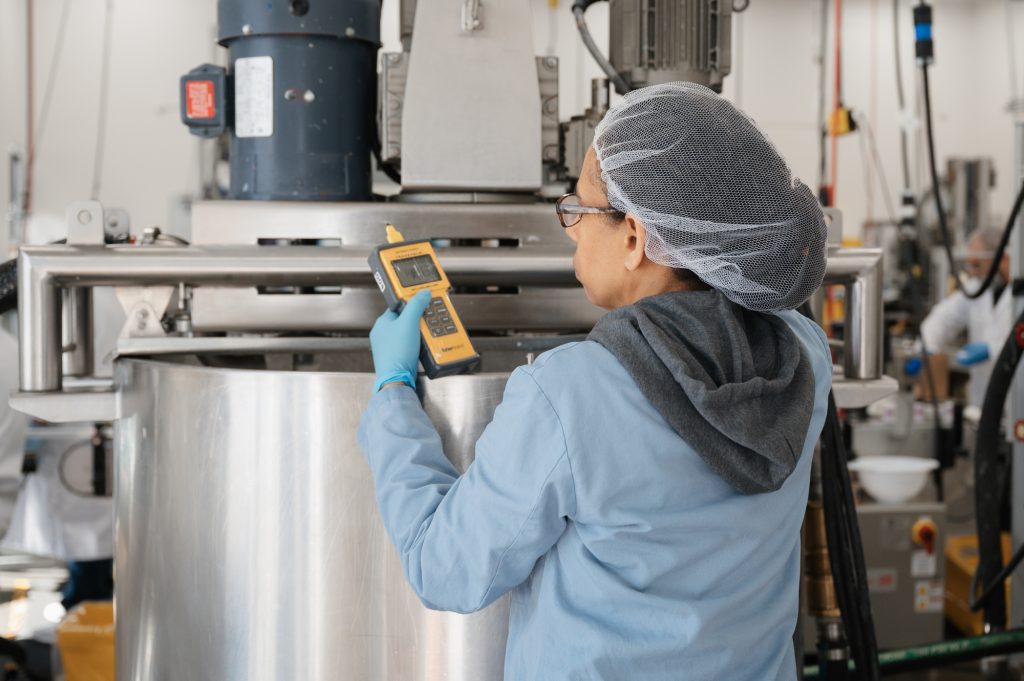
During the initial engineering study, our process engineers ensure that temperatures meet specifications throughout each step of the manufacturing process. Temperatures are confirmed in each step: blending and compounding, the tank temperature while filling, filling nozzle heads, as well as the finished good from initial fill through the cooling stages, to capping and pack out.